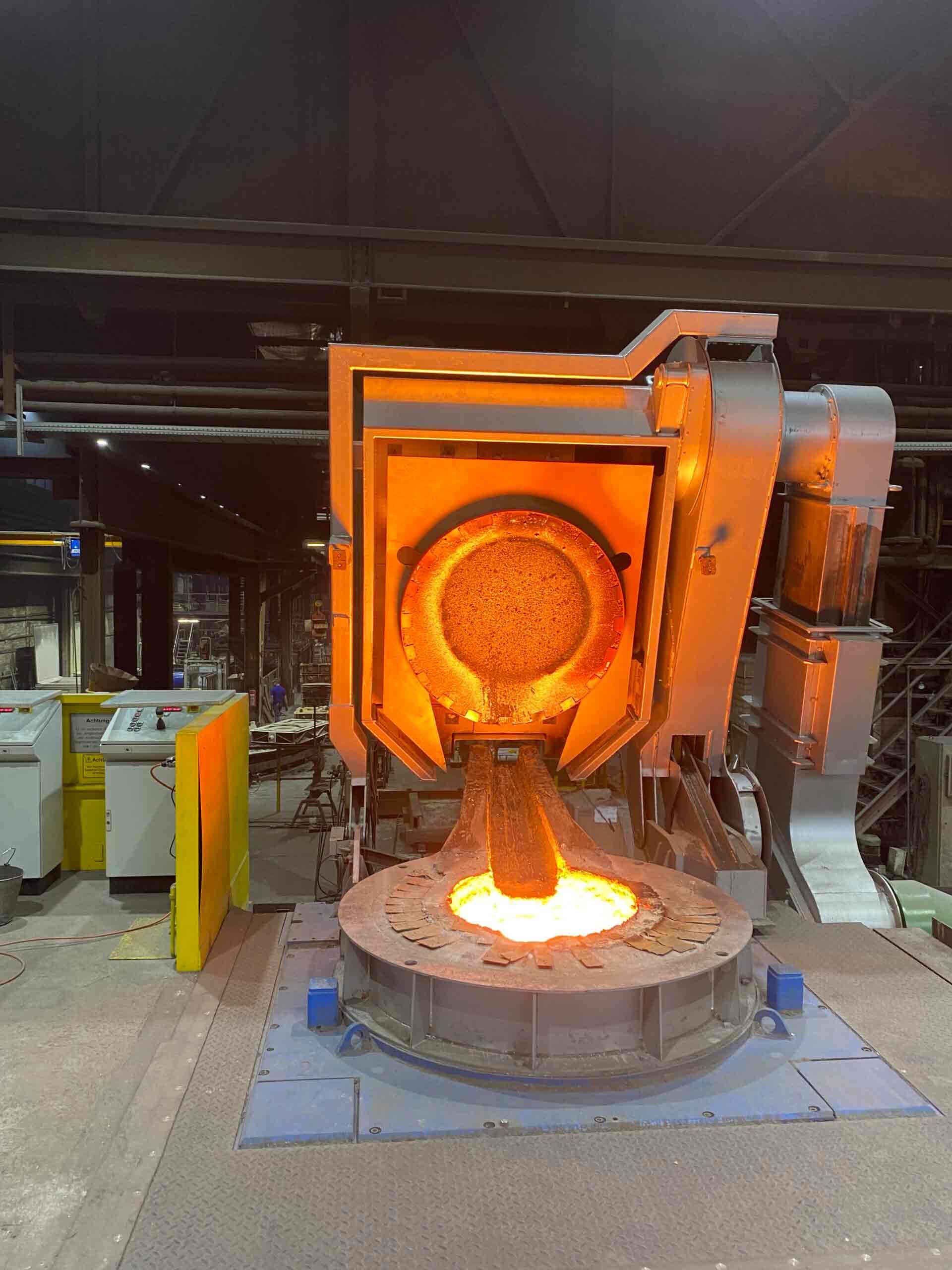
Herzberg, May 22, 2025
Pleissner Guss Invests €6 Million to Support Growth in Rail, Wind Energy, Infrastructure and Defence
Strategic upgrade strengthens portfolio of safety-critical components and high-spec castings for demanding industries
Pleissner Guss GmbH, a GMH Gruppe company, has completed a €6 Million modernisation program aimed at expanding its role as a key supplier to future-critical sectors such as rail technology, wind energy, infrastructure, mechanical engineering and defence. With this investment, the company has upgraded its facilities to produce more advanced and precise castings, including safety-critical components for demanding industrial applications.
“The aim of our investments was to bring the company’s production up to the highest technological standard while ensuring that we are ready for future challenges,” explains Dr Tobias Dubberstein, Managing Director of Pleissner Guss GmbH. ”The improvements make Pleissner Guss more efficient, digitally connected, and sustainable. At the same time, we can now offer a broader range of casting solutions, from large components for wind turbines to safety-critical parts for rail systems and defence technology,” says the managing director.
A major milestone in this upgrade was the implementation of a fully digital metal shop. This system integrates all processes related to melting – from planning and alloy management to batch tracking – creating a smart, data-driven environment that supports precision and traceability across the production chain.
The investment also includes the installation of two modern Medium-frequency induction crucible furnaces with a total casting capacity of 10 tons and a fully electric heat treatment furnace. The existing secondary metallurgy was modernised with a new control system. These new systems significantly reduce energy consumption, eliminate fossil fuel use, and contribute to the GMH Gruppe’s goal of achieving climate-neutral production by 2039. The furnaces are designed for faster and more consistent melting, with lower emissions and minimal wear, which increases operational reliability and product quality.
The modernisation extends to the company’s product capabilities as well. A newly added block casting pit makes it possible to produce large forged and round blocks for high-end industrial uses, such as ring rolling mills and electroslag remelting processes. This positions Pleissner Guss well to meet evolving customer needs in technically demanding markets.
To ensure quality at the highest level, Pleissner Guss has also introduced state-of-the-art inspection technologies. A new optical 3D measurement system allows for precise comparison of cast components with customer CAD data, enabling the accurate inspection of complex geometries. A new, efficient linear accelerator has been added for non-destructive testing. This equipment allows internal defects like cracks or porosity to be detected without damaging the part, increasing the reliability and safety of final products.
In addition, the modernisation included improvements to process control and automation, enhancing both production efficiency and workplace safety. The integration of digital systems across the operation creates a seamless production environment that supports consistent quality and faster delivery.
With these upgrades, Pleissner Guss is now optimally equipped to support customers across Europe with advanced, sustainable, and high-performance casting solutions that are designed for industries which demand, to a special degree, traceability and innovation.
About Pleissner Guss GmbH
Pleissner Guss GmbH, based in Herzberg, Lower Saxony, is one of Europe’s leading steel foundries. The GMH Gruppe company supplies products that are primarily used in valve, pump, and energy machine manufacturing, the railway sector, and general mechanical engineering. It offers a complete range of services, from simultaneous engineering and the creation of the necessary model equipment to mechanical processing on CNC-controlled machines.
About GMH Gruppe
GMH Gruppe is a full-range supplier of steel as a primary material from melted scrap through to ready-to-assemble components. It is one of the largest privately owned metal processing companies in Europe. The group includes 20 medium-sized production companies in the steel, forging and casting industries, which are represented in over 50 countries. With more than 6,000 employees, GMH Gruppe generates an annual turnover of about 2,3 billion euros.
GMH Gruppe is a pioneer in sustainable steel production and has been accepted into the ‘Association of Climate Protection Companies’. Based on the recycling of scrap metal, the company produces green steel and thus makes an important contribution to the circular economy. The use of electric arc furnaces at four sites reduces CO2 emissions by a factor of five compared to conventional blast furnaces. This also reduces the CO2 footprint of the customers supplied by GMH. These include companies worldwide from the automotive industry, mechanical and plant engineering, railway technology, power generation, transport logistics, aerospace, agriculture and construction machinery sectors. GMH Gruppe has set itself the goal of being completely climate-neutral by 2039. Further information can be found at www.gmh-gruppe.de/en/
For inquiries
bmb-consult – PR-Agentur der GMH Gruppe
Simone Boehringer
Senior Editor & Senior Account Manager
GMH Gruppe
Luciana Filizzola
Director Sustainability and Communications