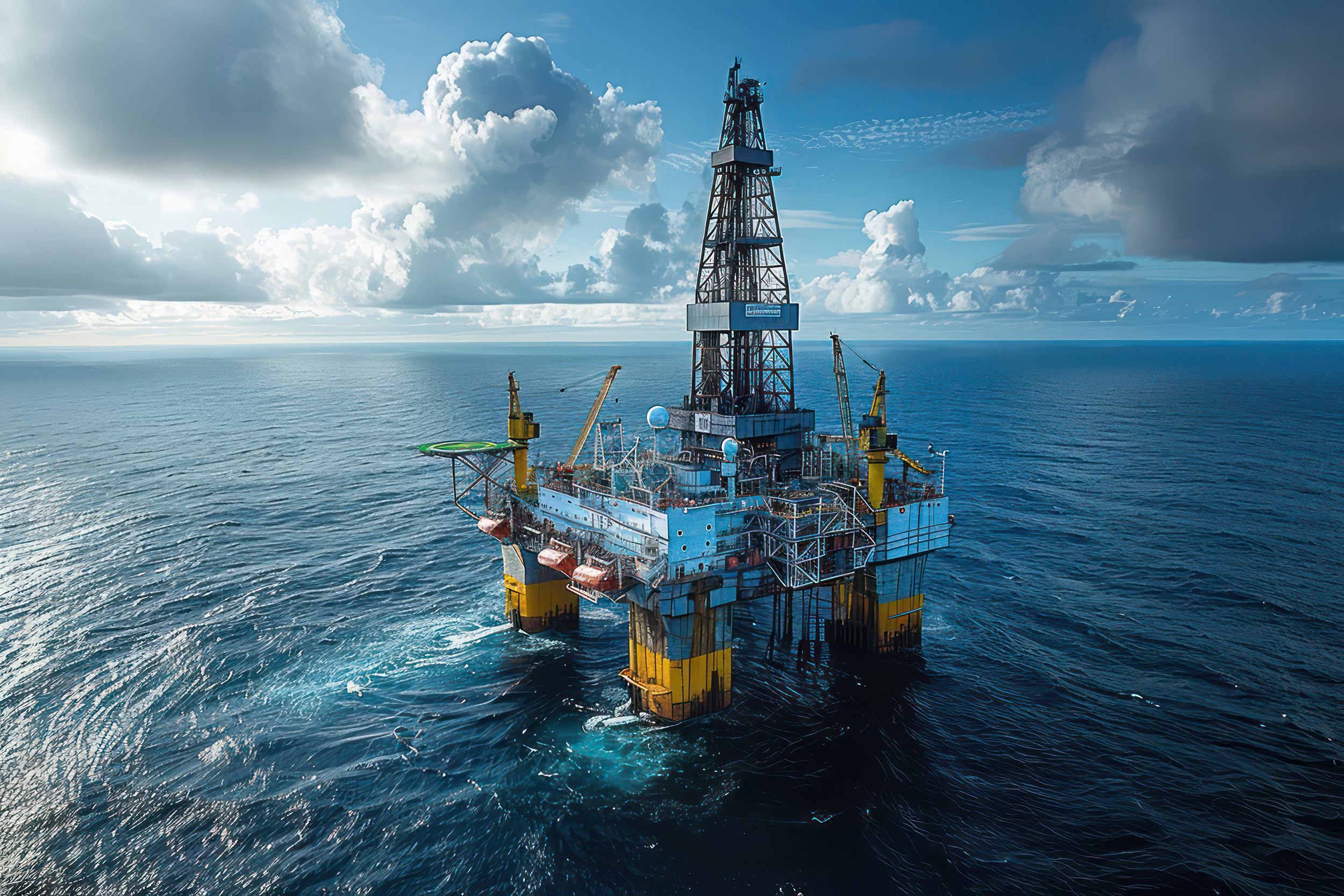
Cronidur® 30 as a Game Changer in the Offshore Sector
Few forces on our planet are as relentless as nature. They push structures and materials to their limits – especially in the depths of the sea. An unmanned offshore platform off the coast of Norway faced precisely this challenge. Its use in the subsea sector required the development of a robust motor-compressor design capable of withstanding extreme underwater conditions.
Challenge: Corrosion Resistance under Extreme Conditions
‘The customer’s components were rusting away,’ recalls the GMH Gruppe team when discussing the start of the collaboration. A replacement for the existing material 1.3505 (100Cr6) was urgently needed – one that could meet the high corrosion resistance requirements of seawater applications. The previously used materials for compressor bearings had proven insufficient under these demanding conditions.
Cronidur® 30: The Key to Success
GMH Gruppe experts quickly identified Cronidur® 30 as the ideal replacement for this project. This high-performance material, rigorously tested and qualified according to strict ISO standards, provided decisive advantages:
- Exceptional corrosion resistance
- Superior durability and toughness,
- Outstanding hardness, ideal for extreme conditions
These properties made Cronidur® 30 the optimal choice for underwater applications.
From Prototypes to Production
Choosing the right material was just the first step. Next, the development of prototype safety bearing bushes and shaft nuts crafted with precision by GMH Gruppe engineers.
Before deployment, the components underwent rigorous testing, including specialized heat treatment developed in collaboration with the customer. This treatment ensured that critical mechanical properties – such as toughness and hardness – were optimized to endure the extreme demands of underwater use. A final quality inspection was conducted directly at Energietechnik Essen GmbH (ETE) to guarantee the highest standards were met.
ETE then supplied bar and bright steel (200-250 mm dimensions) to qualified component manufacturers for final processing.
Extending Maintenance Intervals and Reducing Costs
Thanks to the wear-resistant properties of Cronidur® 30, customers will be able to extend maintenance intervals, reducing the need for costly overhauls of systems operating at depths exceeding 1000 metres. This is not only an economic advantage but also a more sustainable solution.
Looking Ahead: Expanding Cronidur® 30 in the Subsea Sector
Following the positive customer feedback, the project will continue in close collaboration with qualified partners to further expand the use of Cronidur® 30.
With this initiative, GMH Gruppe has successfully established itself in the subsea sector, once again proving exceptional quality and innovative strength of its materials and services.