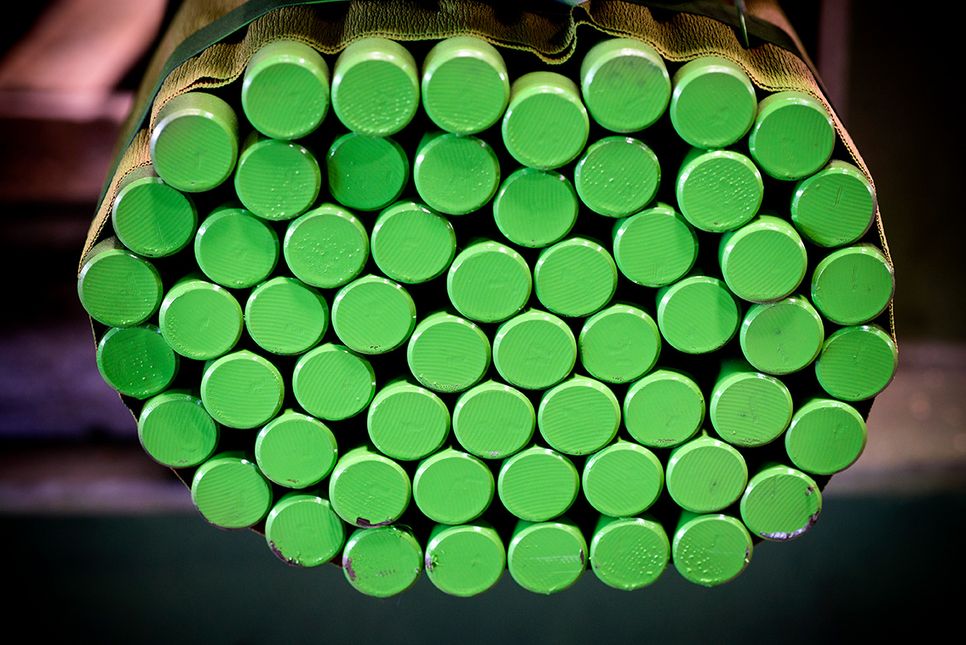
Grüner Stahl für nachhaltige Anwendungen
Die GMH Gruppe hat ein klares Ziel vor Augen: Bis 2039 soll die Stahlproduktion klimaneutral sein. Mit Stahl aus dem Elektrolichtbogenofen und optimierten Prozessen ist dieses Vorhaben realistisch umsetzbar.
Schon frühzeitig hat sich die GMH Gruppe zur Umstellung auf Elektrostahl entschlossen und betreibt aktuell mehrere Ihrer Werke mit Elektrolichtbogenöfen (ELO). Am Standort Georgsmarienhütte wird bereits seit 1994 Qualitäts- und Edelbaustahl mit dem ELO aus 100% Schrott erzeugt. Der entscheidende Vorteil hier: Allein bei der Rohstahlherstellung wird fünfmal weniger CO2 verursacht, als bei der Rohstahlproduktion traditioneller integrierter Hüttenwerke mit Hochofenroute. So steht Elektrostahl für ca. 30 % der Produktion in Deutschland, aber nur für 3 % der Emissionen der Stahlindustrie.
Seit über 25 Jahren vertreibt die GMH Elektrostahl und forciert unter dem Green Steel Label zukunftsorientierte Maßnahmen und Prozesse, um weitere erhebliche Reduzierungen des CO2-Fußabdrucks zu erreichen. Durch den individuellen Einsatz von Strom aus erneuerbaren Energien ist dies bei der GMH heute schon möglich. Bis 2039 soll auf 100 % grünen Strom umgestellt werden und zusätzlich die Verwendung von grünem Wasserstoff anstelle von Erdgas folgen. So kann z. B. auch das Aufwärmen von Blöcken für den Walzprozess oder die Wärmebehandlung von Stabstahl CO2-neutral durchgeführt werden.
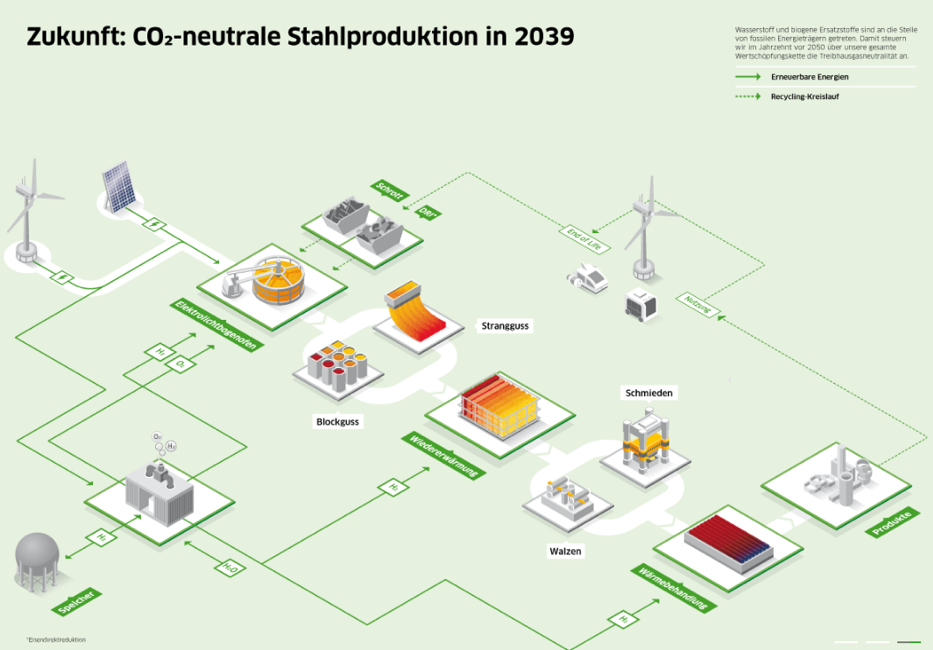
Abbildung 1:
CO2-neutrale Stahlproduktion der GMH Gruppe in 2039.
Neben einer CO2-neutralen Stahlproduktion spielt die Verarbeitung und Anwendung von Stählen ebenfalls eine wesentliche Rolle bei der Energiewende. So können z. B. hochfeste Stähle für den automobilen Leichtbau eingesetzt werden und damit entweder verringerte Kraftstoffverbräuche bei Fahrzeugen mit Verbrennungsmotor oder eine Erhöhung der Reichweite von Elektrofahrzeugen erzielt werden. Auch spielt ein qualitativ hochwertiger Stahl bei der Bauteillebensdauer – und damit für den gesamten Wertstoffkreislauf – eine zentrale Rolle. Je länger der Lebenszyklus eines Bauteiles ist, desto besser ist auch der CO2-Fußabdruck des Endproduktes.
Bei der GMH werden neben Edelbaustählen für Automotive-Anwendungen z. B. auch hochqualitative Werkstoffe für Windenergieanlagen produziert. So stellen langjährige Kunden der GMH bereits seit Jahrzehnten wesentliche Bauteile für On- und Offshore-Anlagen her, z. B. für Rotorblattverstellungen, Getrieberinge oder Flanschwellen, die in den Gondeln der Anlagen verbaut werden. Zudem benötigen leistungsstarke Windkrafträder hochfeste Schrauben und Verbindungselemente für Rotorblätter, Rohr- und Gittermasttürme sowie das Fundament. Der von GMH produzierte Stab- oder Blankstahl wird dabei als Vormaterial entweder in gewalzter/geschälter Ausführung zum Schmieden oder im bereits vergüteten Zustand zur spanenden Herstellung solcher Bauteile geliefert. Der verwendete GMH-Stahl leistet also bereits heute einen wesentlichen Beitrag zum Ausbau der erneuerbaren Energien und zum Schutz unserer Umwelt.
Stahl bietet somit eine der wichtigsten Voraussetzungen zur Reduzierung der CO2-Emissionen entlang der Prozesskette. Für eine möglichst optimale CO2-Bilanz ist jedoch auch die Werkstoffauswahl entscheidend.
CO2-Einsparungen durch Wahl der richtigen Werkstoffe
Anwendungen, insbesondere im Bereich der E-Mobilität, bringen steigende Anforderungen mit sich und erfordern somit neue werkstofftechnische Lösungen. Um diesen Anforderungen an Werkstoffeigenschaften sowie wirtschaftlicher Fertigung gerecht zu werden, optimiert und entwickelt die GMH stetig neue Werkstofflösungen.
Bei der Herstellung von Bauteilen aus Einsatzstählen, wie z. B. Zahnräder und Getriebeteile, ist die Steigerung der Wirtschaftlichkeit und die CO2-Einsparung durch eine Verminderung der Prozessdauer des Einsatzhärtens mittels Hochtemperatur-Aufkohlung möglich. Voraussetzungen dafür sind der Einsatz eines geeigneten Werkstoffes und ein hinreichendes Verständnis vom Einfluss der Prozesskette, um beim Aufkohlen eine ausreichende Feinkornbeständigkeit sicherzustellen. Eine deutliche CO2-Einsparung ist darüber hinaus durch die Nutzung von modernen Vakuumöfen für den Aufkohlungsprozess realisierbar. Insgesamt ergeben sich beim Einsatzhärten damit CO2-Einsparungen von über 50 % im Vergleich zur konventionellen Aufkohlung von Bauteilen.
Die GMH ist zudem Spezialist für Stähle, die ihre finalen Eigenschaften nach geregelter Abkühlung aus der Schmiedehitze erlangen. Durch den Einsatz von diesen ausscheidungshärtenden-ferritisch-perlitischen Stählen (AFP-Stählen), wie z. B. 18MnVS5, 38MnVS6 oder 46MnVS5 sowie bainitischen Stählen wie z. B. dem 16MnCrV7-7, kann auf den Vergütungsprozess verzichtet werden. Diese Prozesseinsparung hat ebenfalls den Vorteil einer deutlichen Reduzierung des CO2-Fußabdruckes.
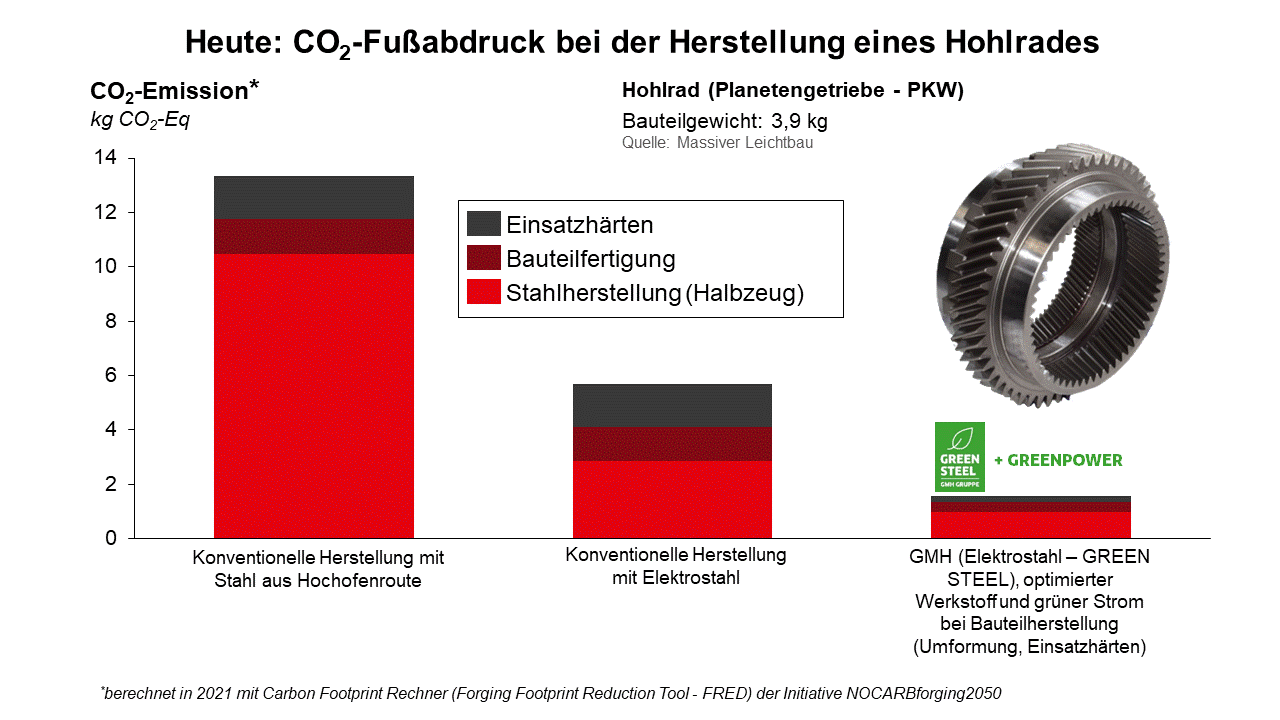
Abbildung 2:
Optimierung des CO2-Fußabdruckes bei der Herstellung eines Hohlrades
Berücksichtigung des gesamten Herstellungsprozesses
Neben der Vormaterialherstellung ist auch die eigentliche Fertigung der Bauteile durch Umformung, zusätzliche Wärmebehandlung und Endbearbeitung sehr energieaufwendig. Im obigen Diagramm, Abbildung 2, ist beispielhaft der CO2-Fußabdruck bei der Herstellung eines Hohlrades (PKW-Getriebe) dargestellt. Dabei wurden die drei Prozessschritte Vormaterial- und Bauteilherstellung sowie das abschließende Einsatzhärten mit Hilfe des FRED-Tools (Forging Footprint Reduction Tool) aus dem Projekt NOCARB-forging2050 des Industrieverbandes Massivumformung (IMU) berücksichtigt. Hierbei wird deutlich, dass durch die Verwendung des GMH-Elektrostahls ein wesentlicher Teil der CO2-Emissionen reduziert werden kann. Durch die Verwendung von grünem Strom, einem optimierten Werkstoff sowie modernen Aufkohlungsöfen sind darüber hinaus weitere erhebliche Einsparungen von CO2 realisierbar. So ist technologisch bereits heute eine Reduzierung von insgesamt über 80 % des CO2-Fußabdrucks bei der Herstellung von Bauteilen aus Stahl möglich. Das ambitionierte Ziel: Vollständige Klimaneutralität durch den Einsatz von Wasserstoff bis spätestens 2039.